In a warehouse larger than three football fields, 3,000 bots scuttle along at 13 feet per second, swerving to avoid each other in a complex dance governed by artificial intelligence. Their goal? To get your groceries much faster than humanly possible.
The south-east London warehouse is run by British online supermarket Ocado and features the latest in its automation technology. The company started out developing the Ocado Smart Platform (OSP) for its own use, but the systemhas proved so successful it licenses it to other supermarkets.
Playing chicken with robots
The bots – which look like washing machines on wheels – move on top of a grid, like pieces on a chessboard. Beneath the floor, each square hides a stack up to 21 containers deep. The containers are filled with some of the 50,000 products offered by Ocado, stored according to an algorithm that predicts when they will be needed.
When an order is sent to the warehouse, the bots spring to life and head towards the container they require, passing within five millimeters of each other.
“We basically play chicken with them: they go on a collision course only to divert at the last moment,” says Alex Harvey, chief of advanced technology at Ocado Technology.
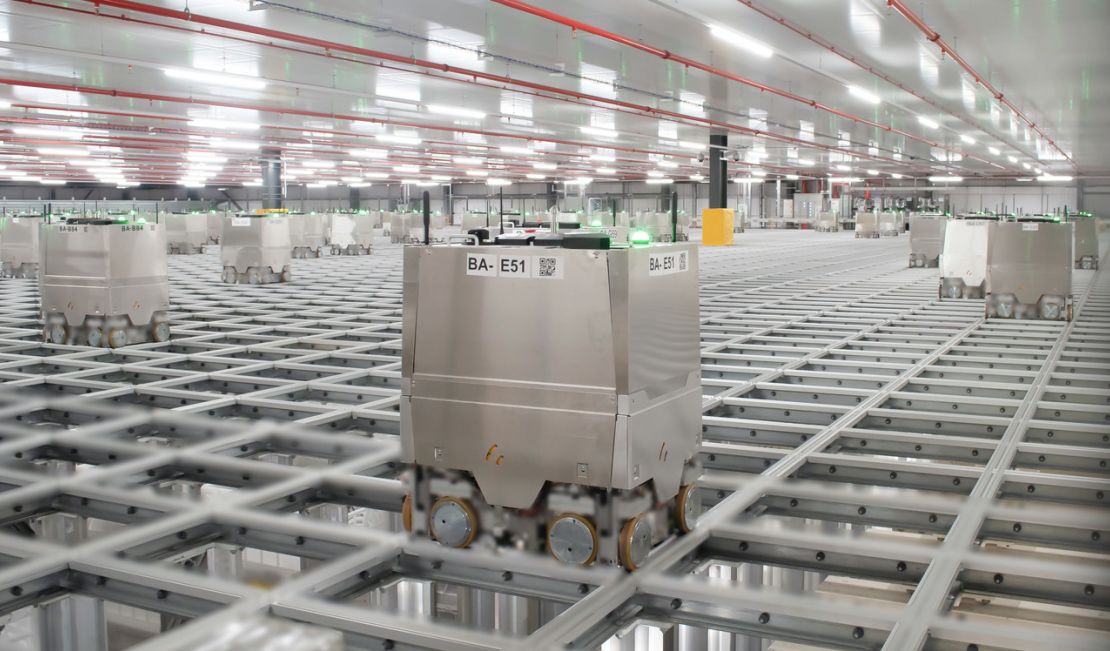
The bots are not autonomous but orchestrated by a system that works like air traffic control, planning their routes for them. Armed with a grabbing mechanism, the bots can pick up one container each. If a product is stored five containers down, for example, four bots will first remove the containers above it, clearing the way for a “hero” bot that is fulfilling an order.
Once the “hero” bot has grasped a container, it takes it to a picking station, where a person (or another robot, depending on the technology installed in each warehouse) will select the item and add it to an order. The finished order is then moved – by bots – to a van for delivery.
Improving accuracy, cutting waste
When Ocado launched 21 years ago, it used a more traditional system of conveyor belts and cranes, similar to the ones used for handling luggage in airports. This type of system is prone to congestion. “One order can take over three hours to pick, because delivery containers have to wind their way around over 15 miles on conveyor belts,” says Harvey. “The new system can pick an entire order in less than 15 minutes.”
OSP, which was launched six years ago, has other advantages according to Simon Mayhew, an analyst at British market research firm IGD, who is unaffiliated with Ocado: “Its order accuracy tracks at 99%, and its fulfilment centers use a first-in, first-out approach,” he says, so food is fresher and waste is minimized.
Mayhew estimates most good retailers achieve 97% to 98% order accuracy. Ocado’s might seem like a small improvement, but it can make a big difference in terms of convenience and shopper experience, he says.
However, Mayhew notes that building Ocado’s large fulfilment centers is a slow process, and they cater only to online shopping. Some other retailers have built micro-fulfilment centers inside retail stores. Although they can’t handle as many orders they deliver them more quickly, because they are close to shoppers’ homes.
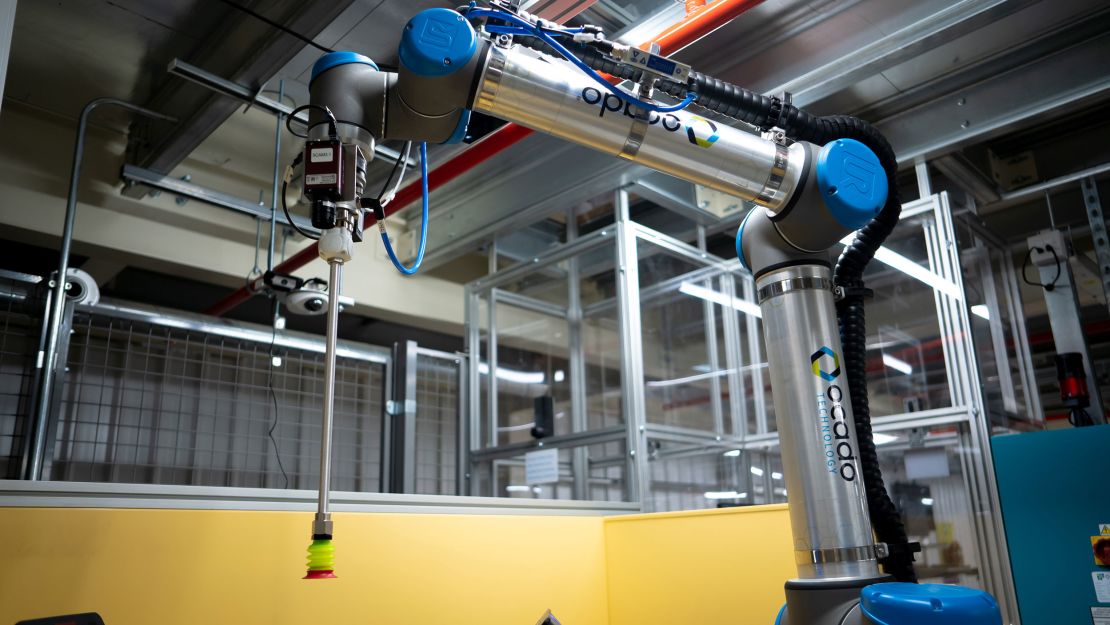
Now a fully-fledged tech company, as well as an online shop, Ocado has licensed OSP to several major grocers around the world, including Kroger in the US, Casino in France and Coles in Australia, through deals based on revenue sharing. A publicly traded company, Ocado has a stock market valuation of over $22 billion.
The company says that at 563,000 square feet, its south-east London premises is the largest automated warehouse for groceries in the world.
Ocado is pursuing even more automation. Currently, most of the picking – the final stage of an order in which items are placed in bags – is still done by humans, but the company has started using robotic arms. Last year, it spent nearly $300 million acquiring two US companies, Kindred Systems and Haddington Dynamics, to increase its expertise in robotic arms and sorting systems.
“Labor costs are one of the key driving factors in the cost of groceries,” says Harvey, “and our goal is to try to automate these very repetitive, not particularly exciting human operations in the warehouse.”
Critics of automation point to its impact on employment opportunities. Up to 20 million manufacturing jobs around the world could be lost to robots by 2030, according to market forecasting company Oxford Economics.
Harvey says that when Ocado builds new facilities for international retailers from scratch, it creates jobs that didn’t exist before. In existing facilities where picking is becoming automated, for example, the company has retrained human pickers to supervise the robots instead.
The ultimate goal, however, is a warehouse run entirely by robots, Harvey says. “The vision we have is being able to receive groceries in the warehouse, do all the putting away, and then do all the picking and deliver them out the door without a single human touch.”